From the user perspective, many believe that only heavier vibratory rollers provide better compaction capacity and effect.
From the manufacturers’ side, heavier vibratory rollers are priced higher. To meet demand and remain competitive, Chinese manufacturers have pushed for larger-tonnage rollers. Single-drum vibratory rollers have increased from 18, 20, 22, 25, 27, and 32 tons to 36 tons. Double-drum rollers have gone from 12 and 13 tons to 16 tons.
What about actual application?
In the early 20th century, industrialized countries like the USA and some in Europe completed their highway networks using single-drum vibratory rollers under 20 tons and double-drum rollers under 12 tons. Their highways are no less quality than China’s.
Before entering the Chinese market, renowned global roller manufacturers also did not have single-drum rollers over 20 tons or double-drum rollers over 12 tons. Hence, our current rollers should meet construction needs fully.
Developing some large-tonnage rollers is reasonable, but we shouldn’t do so blindly. Heavier rollers consume more resources and energy, raising construction costs. Especially for double-drum rollers, too heavy a machine may crush aggregates, reducing construction quality.
Factors affecting compaction capacity and effect include more than just weight—vibration parameters, vibration mode, and working speed are crucial. We can enhance compaction through these means. For instance, tests have shown that a 20-ton fully hydraulic single-drum vertical vibratory roller performs better than a 32-ton mechanical roller. Let’s not rely solely on weight to improve efficiency and results.
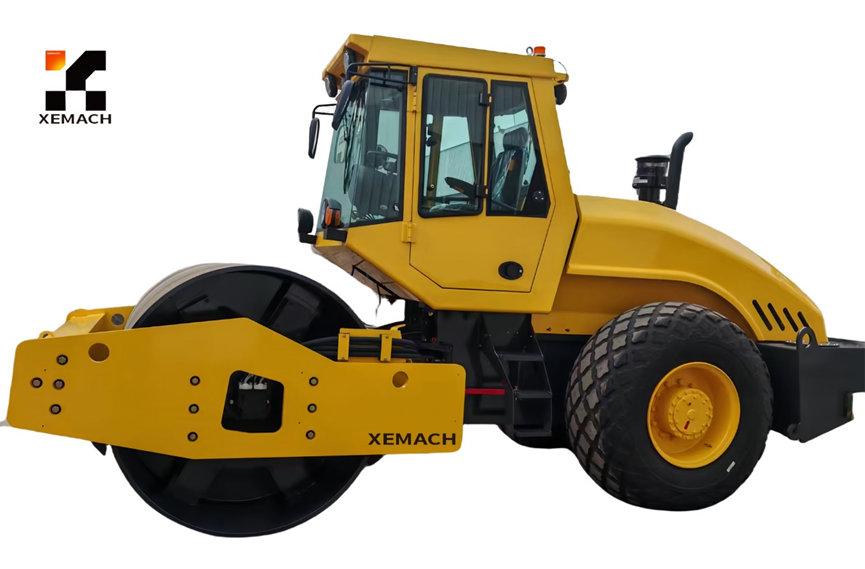